Cryogenic Butterfly Valve
CRYOGENIC BUTTERFLY VALVE: Engineered for Extreme Cold & Uncompromising Reliability
Conquer the challenges of ultra-low temperature applications with our precision-engineered Cryogenic Butterfly Valve. Designed specifically for the demanding environments of LNG (Liquefied Natural Gas), liquid nitrogen, oxygen, argon, CO2, and other cryogenic fluids, this valve delivers exceptional performance, safety, and longevity where standard valves fail.
Technical parameters of cryogenic butterfly valve
Nominal size | NPS 1/2″ – 48″ (DN15 -1200 mm) |
Nominal pressure | Class 150, 300, 600Lb, 900LB, 1500LB |
End Connection | Flange RF, Flange RTJ, BW, SW, NPT, etc. |
Operation | Lever, Gear Box, Pneumatic Actuator, Electric Actuator |
Material | Carbon Stee: LCB (-46℃), LC3 (-101℃) .Stainless Steel: CF8 (-196℃), CF8M, CF3, CF3M.
Duplex Stainless Steel: 4A, 5A, 6A. |
Using temperature | -46℃, -101℃, -196℃, -253℃. |
Applicable medium | Liquefied natural gas (LGN), ethylene, propylene, medicine, aerospace, etc. |
Design standard | API6D, BS6364, MSS SP-134 |
Face to Face | ASME B16.34, ASME B16.10 |
Connection standard | ASME B16.5, ASME B16.47 |
Test standard | API 598 |
Other standards | API 624, ISO 15848-1, ISO 15848-2, API 607, API 6FA |
Tips: Cryogenic valve manufacturing and testing
Cryogenic valves require strict quality control of parts processing.
1. Special cryogenic treatment: the rough-machined parts are placed in the cooling medium for several hours (2-6 hours) to release stress, ensure the low-temperature performance of the material, and ensure the fine processing size to prevent the valve from leaking due to deformation caused by temperature changes when working under low-temperature conditions.
2. Impact test: After the valve parts have completed the cryogenic treatment, they need to undergo a low-temperature impact test, and they can only be assembled after the test is qualified.
3. Valve Parts Cleaning: The assembly of the valve is also different from that of ordinary valves. The parts of the valve need to be strictly cleaned to remove any oil stains to ensure performance.
4. Nitrogen test: After the valve is assembled, a low-temperature test is required. The medium for low-temperature testing is different from that of conventional valves, and nitrogen needs to be used for testing.
Why Choose Our Cryogenic Butterfly Valve
Unmatched Cold Performance: Built to operate flawlessly at temperatures plunging down to -196°C (-320°F) and beyond. Every component, from body to disc to seat, is meticulously selected and treated to withstand extreme thermal contraction without compromising integrity.
Advanced Extended Bonnet Design:
Our critical long stem extension (extended bonnet) acts as a thermal barrier. This ingenious feature:
• Prevents Seat Freezing: Keeps critical sealing components away from the intense cold path.
• Protects Stem Packing: Ensures reliable stem sealing by maintaining packing at ambient temperatures, preventing brittleness and leakage.
• Safeguards Actuators: Allows standard actuators to operate effectively without exposure to cryogenic temperatures.
• Leak-Tight Security: Achieves bubble-tight shut-off (BS 6364 compliant) in both flow directions. Our specialized low-temperature seat materials provide exceptional sealing integrity, minimizing fugitive emissions and ensuring process safety in critical cryogenic systems.
Superior Materials & Construction:
• Body & Disc: High-integrity materials like Stainless Steel (CF8M/SS316) or Duplex Stainless Steel, often cryogenically treated to enhance toughness at low temperatures.
• Seat: Engineered polymers (e.g., RPTFE, PCTFE, PEEK) or resilient metal seats, specifically chosen for their outstanding resilience and sealing performance in extreme cold.
• Stem: Robust design, often using materials like Stainless Steel 316 or 17-4PH, precisely machined for smooth, reliable operation.
• BS 6364 Compliance: Manufactured and tested in accordance with the stringent BS 6364 standard for cryogenic valves, guaranteeing performance, safety, and reliability under deep cryogenic conditions.
• Robust & Efficient Operation: Features a low operating torque design, ensuring smooth actuation even at cryogenic temperatures. Compatible with manual levers, gearboxes, pneumatic actuators, or electric actuators for seamless integration into your control system.
Versatile Applications:
The ideal solution for:
→ LNG Production, Storage & Transfer: Terminals, tanker loading/unloading, vaporizers.
→ Industrial Gas Processing: Nitrogen, oxygen, argon plants.
→ Cryogenic Storage Tanks & Vessels.
→ Aerospace & Defense Testing.
→ Chemical Processing (Cryogenic stages).
→ Medical & Pharmaceutical (Liquid gases).
Engineered for Safety & Long-Term Value:
Zero Fugitive Emissions: Designed to meet stringent environmental and safety regulations.
Minimal Maintenance: Robust construction and high-quality materials ensure a long service life, reducing downtime and total cost of ownership.
Proven Reliability: Built to perform in the world’s most critical cryogenic infrastructure.
Find Your Cryogenic Solution:
Whether you’re managing LNG flow, handling liquid gases, or operating in any ultra-low temperature environment, our Cryogenic Butterfly Valve provides the dependable, leak-tight performance you demand. Experience the difference precision engineering makes at cryogenic extremes.
Optimize your cryogenic process safety and efficiency. Request a quote or download the detailed datasheet for our BS 6364 compliant Cryogenic Butterfly Valves today!
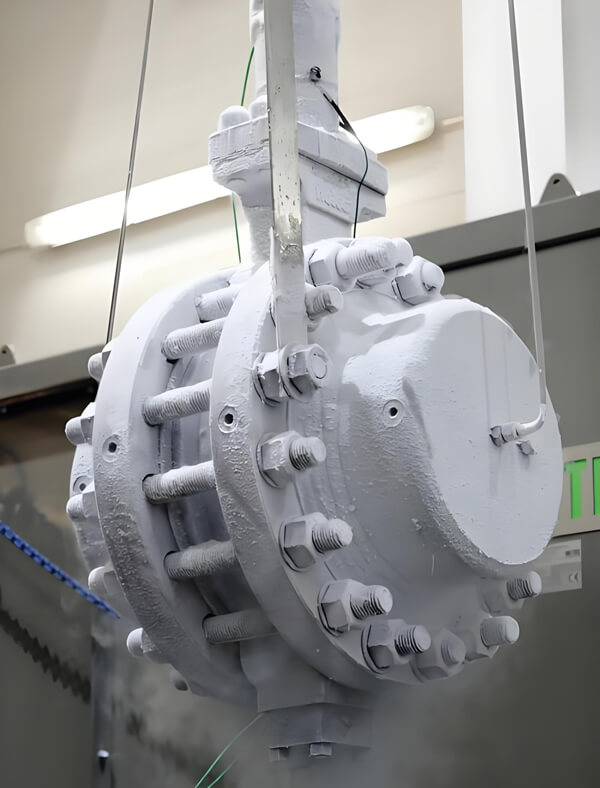
Materials of Newsway Valve Manufacturer Products
The China Valve Manufacturer from China, its valves body and trim material can be offered in Forged type and Casting type. Next to Stainless Steel and Carbon Steel material, we also manufacture valves in special materials such as titanium, nickel alloys, HASTELLOY®*, INCOLOY®, MONEL®, Alloy 20, super-duplex, corrosion resistant alloys and urea grade materials.
Available Valve Materials
Tradename | UNS nr. | Werkstoff nr. | Forging | Casting |
Carbon steel | K30504 | 1.0402 | A105 | A216 WCB |
Carbon steel | 1.046 | A105N | ||
Low Temp Carbon steel | K03011 | 1.0508 | A350 LF2 | A352 LCB |
High Yield steel | K03014 | A694 F60 | ||
3 1/2 Nickel steel | K32025 | 1.5639 | A350 LF3 | A352 LC3 |
5 Chrome, 1/2 Moly | K41545 | 1.7362 | A182 F5 | A217 C5 |
1 1/4 Chrome, 1/2 Moly | K11572 | 1.7733 | A182 F11 | A217 WC6 |
K11597 | 1.7335 | |||
2 1/4 Chrome, 1/2 Moly | K21590 | 1.738 | A182 F22 | A217 WC9 |
9 Chrome, 1 Moly | K90941 | 1.7386 | A182 F9 | A217 CW6 |
X 12 Chrome, 091 Moly | K91560 | 1.4903 | A182 F91 | A217 C12 |
13 Chrome | S41000 | A182 F6A | A351 CA15 | |
17-4PH | S17400 | 1.4542 | A564 630 | |
254 SMo | S31254 | 1.4547 | A182 F44 | A351 CK3MCuN |
304 | S30400 | 1.4301 | A182 F304 | A351 CF8 |
304L | S30403 | 1.4306 | A182 F304L | A351 CF3 |
310S | S31008 | 1.4845 | A182 F310S | A351 CK20 |
316 | S31600 | 1.4401 | A182 F316 | A351 CF8M |
S31600 | 1.4436 | |||
316L | S31603 | 1.4404 | A182 F316L | A351 CF3M |
316Ti | S31635 | 1.4571 | A182 F316Ti | |
317L | S31703 | 1.4438 | A182 F317L | A351CG8M |
321 | S32100 | 1.4541 | A182 F321 | |
321H | S32109 | 1.4878 | A182 F321H | |
347 | S34700 | 1.455 | A182 F347 | A351 CF8C |
347H | S34709 | 1.4961 | A182 F347H | |
410 | S41000 | 1.4006 | A182 F410 | |
904L | N08904 | 1.4539 | A182 F904L | |
Carpenter 20 | N08020 | 2.466 | B462 N08020 | A351 CN7M |
Duplex 4462 | S31803 | 1.4462 | A182 F51 | A890 Gr 4A |
SAF 2507 | S32750 | 1.4469 | A182 F53 | A890 Gr 6A |
Zeron 100 | S32760 | 1.4501 | A182 F55 | A351 GR CD3MWCuN |
Ferralium® 255 | S32550 | 1.4507 | A182 F61 | |
Nicrofer 5923 hMo | N06059 | 2.4605 | B462 N06059 | |
Nickel 200 | N02200 | 2.4066 | B564 N02200 | |
Nickel 201 | N02201 | 2.4068 | B564 N02201 | |
Monel® 400 | N04400 | 2.436 | B564 N04400 | A494 M35-1 |
Monel® K500 | N05500 | 2.4375 | B865 N05500 | |
Incoloy® 800 | N08800 | 1.4876 | B564 N08800 | |
Incoloy® 800H | N08810 | 1.4958 | B564 N08810 | |
Incoloy® 800HT | N08811 | 1.4959 | B564 N08811 | |
Incoloy® 825 | N08825 | 2.4858 | B564 N08825 | |
Inconel® 600 | N06600 | 2.4816 | B564 N06600 | A494 CY40 |
Inconel® 625 | N06625 | 2.4856 | B564 N06625 | A494 CW 6MC |
Hastelloy® B2 | N10665 | 2.4617 | B564 N10665 | A494 N 12MV |
Hastelloy® B3 | N10675 | 2.46 | B564 N10675 | |
Hastelloy® C22 | N06022 | 2.4602 | B574 N06022 | A494 CX2MW |
Hastelloy® C276 | N10276 | 2.4819 | B564 N10276 | |
Hastelloy® C4 | N06455 | 2.461 | B574 N06455 | |
Titanium GR. 1 | R50250 | 3.7025 | B381 F1 | B367 C1 |
Titanium GR. 2 | R50400 | 3.7035 | B381 F2 | B367 C2 |
Titanium GR. 3 | R50550 | 3.7055 | B381 F3 | B367 C3 |
Titanium GR. 5 | R56400 | 3.7165 | B381 F5 | B367 C5 |
Titanium GR. 7 | R52400 | 3.7235 | B381 F7 | B367 C7 |
Titanium GR. 12 | R53400 | 3.7225 | B381 F12 | B367 C12 |
Zirconium® 702 | R60702 | B493 R60702 | ||
Zirconium® 705 | R60705 | B493 R60705 |